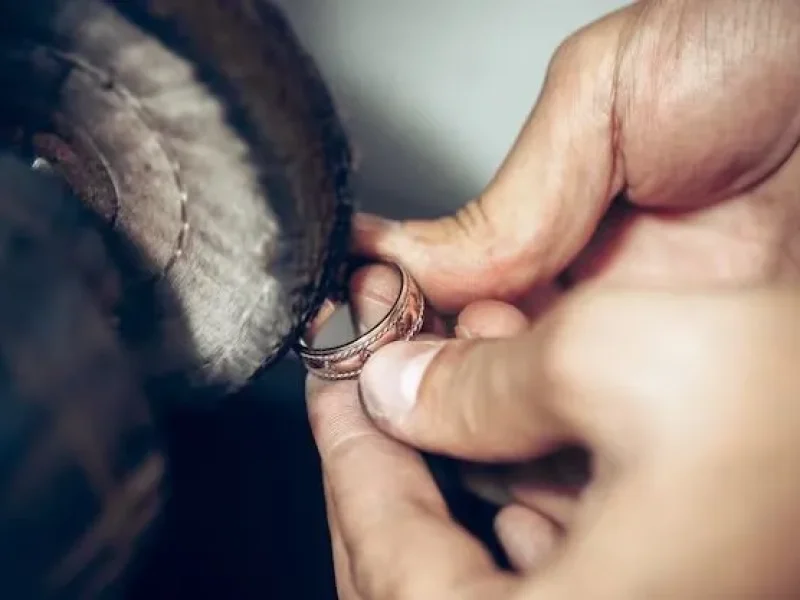
- Jewelry Market
Crafting Classics: Traditional Jewelry Making Techniques
Table of Contents
1- Casting: A Timeless Technique in Jewelry Making
Casting is a fundamental technique in jewelry design that has been used for centuries to create intricate and detailed pieces. This process involves melting metal and pouring it into a mold to form a specific shape.
1.1.casting process:
1. Model Creation: The first step is to create a model of the desired jewelry piece. This can be done using various materials, such as wax, clay, or resin. The model serves as a template for the final casting.
2. Mold Preparation: Once the model is complete, it is encased in a mold. This mold is typically made from a heat-resistant material like plaster or ceramic.
3. Melting Metal: The metal chosen for the casting is melted in a furnace until it reaches a liquid state. The type of metal used will depend on the desired properties of the final piece, such as durability and cost.
4. Pouring: The molten metal is carefully poured into the mold cavity, filling it completely. The metal will take the shape of the cavity as it cools and solidifies.
5. Removal: After the metal has cooled, the mold is removed. The cast piece is then revealed, showcasing the intricate details of the original model.
6. Finishing: The cast piece may require additional finishing work to achieve the desired look. This can include polishing, engraving, or setting gemstones.
2.1.Advantages of Casting:
• Intricate Designs: Casting allows for the creation of highly detailed and complex jewelry pieces.
• Mass Production: This technique is well-suited for mass production of jewelry, making it a popular choice for commercial jewelers.
• Variety of Metals: Casting can be used with a wide range of metals, including precious metals like gold and silver, as well as base metals like brass and pewter.
Casting is a versatile and time-honored technique that continues to be used in jewelry making today. It allows for the creation of stunning and unique pieces that showcase the skill and artistry of the jeweler.
From: cdocast.com/
2. Soldering
Soldering is a process used to join two or more metal pieces together by melting a lower-melting-point metal alloy, called solder, between the pieces and allowing it to bond to them as it cools. This process is often used in electronics, plumbing, and jewelry making.
1.2.The Soldering Process
1. Preparation:
o Clean the surfaces: Ensure the metal surfaces to be joined are clean and free of contaminants like grease, dirt, or oxidation. This is crucial for the solder to adhere properly.
o Flux application: A flux is a chemical substance that helps remove oxides from the metal surfaces and promotes the wetting of the metal by the solder. It can be applied in various forms, such as a paste, liquid, or powder.
2. Heating:
o Heat source: A soldering iron or a soldering gun is typically used to heat the metal pieces and the solder. The temperature of the heat source should be high enough to melt the solder but not so high that it damages the metal or the surrounding components.
3. Applying Solder:
o Touch the solder: Once the metal pieces are sufficiently heated, the tip of the soldering iron or gun is touched to the solder. The heat from the iron will cause the solder to melt.
o Feed the solder: As the solder melts, it is fed into the joint between the metal pieces. The solder should flow smoothly and evenly into the joint, creating a strong bond.
4. Cooling:
o Allow to cool: Once the solder has filled the joint, the heat source is removed, and the joint is allowed to cool undisturbed. As the solder cools, it solidifies and forms a strong bond between the metal pieces.
2.2.Types of Solder
• Soft solder: This is a low-melting-point alloy, typically composed of tin and lead. It is commonly used in electronics and plumbing applications.
• Hard solder: This is a higher-melting-point alloy, often containing silver, copper, and zinc. It is used in applications where a stronger and more heat-resistant joint is required, such as in jewelry making and industrial metalworking.
3.2.Applications of Soldering
• Electronics: Soldering is essential for connecting components in electronic circuits, such as resistors, capacitors, and integrated circuits.
• Plumbing: Soldering is used to join copper pipes in plumbing systems, ensuring a leak-free connection.
• Jewelry making: Soldering is used to join precious metals, such as gold and silver, in the creation of jewelry pieces.
• Industrial metalworking: Soldering is used in various industrial applications, such as repairing metal structures and fabricating metal components.
By understanding the soldering process and the different types of solder, you can effectively use this technique to join metal pieces in various applications.
3. Engraving: Carving Designs Into Metal Using a Burin
Engraving is the art of cutting or carving designs into metal, typically using a sharp tool called a burin. This technique has been used for centuries to create intricate patterns, inscriptions, and images on a variety of metal objects, including jewelry, silverware, and decorative items.
1.3.The Engraving Process
1. Design Preparation:
o Sketching: The desired design is often sketched onto the metal surface. This can be done directly or using a transfer paper.
o Tracing: If a transfer paper is used, the design is traced onto the metal surface.
2. Burin Selection:
o Burin choice: The appropriate burin is selected based on the type of design and the hardness of the metal. Burins come in various shapes and sizes, each designed for specific tasks.
3. Engraving:
o Cutting: The burin is held at an angle and used to cut into the metal surface, creating the desired design. The burin is pushed forward with firm pressure, removing material and forming the desired shape.
o Depth control: The depth of the engraving can be controlled by adjusting the pressure applied to the burin. A shallow engraving can create a delicate effect, while a deeper engraving can provide more contrast.
4. Finishing:
o Polishing: Once the engraving is complete, the metal surface may be polished to remove any burrs or imperfections. This can enhance the appearance of the engraving and give it a finished look.
2.3.Types of Engraving
• Line engraving: This technique involves creating a series of fine lines to form the design. It is often used for intricate patterns and inscriptions.
• Relief engraving: In this technique, the design is raised above the surrounding metal surface. This creates a three-dimensional effect and is often used for decorative purposes.
• Intaglio engraving: This technique involves cutting the design below the surrounding metal surface. This creates a recessed design that can be filled with enamel or other materials.
3.3.Applications of Engraving
• Jewelry: Engraving is commonly used to personalize jewelry pieces with names, dates, or special messages.
• Silverware: Silverware is often engraved with intricate patterns or family crests.
• Decorative items: Metal objects such as vases, bowls, and plaques can be engraved with designs or inscriptions.
• Industrial applications: Engraving is used in various industrial applications, such as marking tools, machinery, and metal components.
Engraving is a skilled craft that requires precision, patience, and a good understanding of metalworking techniques. The ability to create intricate and beautiful designs on metal surfaces has made engraving a valuable art form for centuries.
4.Setting: Securing Gemstones into Metal Settings
Setting is the process of securing a gemstone into a metal mount or setting. This is a crucial step in jewelry making, as it ensures that the gemstone is held securely in place and protected from damage.
Types of Settings
There are several different types of settings used in jewelry making, each with its own advantages and disadvantages:
• Prong setting: In this type of setting, the gemstone is held in place by metal prongs that are bent over the edges of the stone. This setting provides good visibility of the gemstone and is often used for larger stones.
Prong setting in jewelry
• Bezel setting: In this setting, the gemstone is surrounded by a thin metal band or bezel that is formed to fit the shape of the stone. This setting provides excellent protection for the gemstone and is often used for smaller stones.
Bezel setting in jewelry
• Channel setting: In this setting, the gemstone is set into a channel that is cut into the metal. This setting is often used for multiple stones that are set side by side.
Channel setting in jewelry
• Pavé setting: In this setting, a large number of small gemstones are set closely together, creating a sparkling and luxurious effect.
Pavé setting in jewelry
• Invisible setting: In this setting, the gemstones are set so that the metal setting is not visible, creating a seamless and illusionary effect.
Invisible setting in jewelry
The Setting Process
The setting process involves several steps:
1. Preparing the setting: The metal setting is prepared by cutting and shaping it to fit the gemstone.
2. Placing the gemstone: The gemstone is carefully placed into the setting.
3. Securing the gemstone: The setting is then secured around the gemstone using various techniques, such as soldering, hammering, or crimping.
4. Finishing: The setting is finished by polishing and buffing it to remove any scratches or imperfections.
Factors to Consider When Choosing a Setting
When choosing a setting for a gemstone, several factors should be considered:
• The shape of the gemstone: The setting should be designed to complement the shape of the gemstone.
• The size of the gemstone: Larger gemstones may require a more robust setting to ensure that they are held securely in place.
• The desired level of protection: Some settings provide better protection for the gemstone than others.
• The overall style of the jewelry: The setting should complement the overall style of the jewelry piece.
By understanding the different types of settings and the factors to consider when choosing a setting, you can ensure that your gemstones are set securely and beautifully.
4.4. Beading
Beading
Beading is a popular craft involving the art of stringing beads together to create various pieces, such as necklaces, bracelets, earrings, and anklets. This versatile technique allows for the creation of unique and personalized jewelry, as well as decorative objects.
The Beading Process
1. Choosing Materials:
o Beads: Beads come in a wide variety of materials, including glass, ceramic, plastic, metal, and gemstones. The choice of beads will depend on the desired look, durability, and budget.
o Stringing material: The most common stringing materials are thread, wire, and cord. The choice of stringing material will depend on the size and weight of the beads, as well as the desired style of the piece.
2. Designing:
o Planning the piece: Before starting, it’s essential to plan the desired design. This may involve sketching or creating a pattern.
o Choosing colors and styles: The choice of colors and styles will depend on personal preference and the intended use of the piece.
3. Stringing the Beads:
o Threading the beads: The beads are threaded onto the stringing material in the desired order.
o Creating patterns: Patterns can be created by using different sizes, shapes, and colors of beads.
o Securing the ends: Once the beads are strung, the ends of the stringing material are secured to prevent the beads from falling off. This can be done using knots, clasps, or other methods.
4. Finishing:
o Adding embellishments: Additional embellishments, such as charms, pendants, or tassels, can be added to enhance the appearance of the piece.
o Cleaning and polishing: The finished piece can be cleaned and polished to remove any dirt or fingerprints.
Types of Beading Techniques
• Stringing: The most basic form of beading, involving threading beads onto a stringing material.
• Kumihimo: A Japanese braiding technique that uses a special tool called a kumihimo disk to create intricate patterns.
• Peyote stitch: A technique that involves weaving beads together to create a flat, fabric-like piece.
• Brick stitch: A technique that involves weaving beads together to create a raised, textured piece.
Applications of Beading
• Jewelry: Beading is commonly used to create necklaces, bracelets, earrings, and other jewelry pieces.
• Home decor: Beaded items can be used to decorate homes, such as curtains, pillows, and wall hangings.
• Accessories: Beading can be used to create accessories, such as belts, bags, and bookmarks.
• Art: Beading can be used to create art pieces, such as sculptures and mosaics.
Beading is a versatile and enjoyable craft that allows for the creation of unique and personalized pieces. With a little practice and creativity, anyone can learn to bead and create beautiful works of art.
3- Wirework: Shaping and Bending Wire to Create Intricate Designs
Wirework is a versatile craft that involves shaping and bending wire to create intricate designs. This technique can be used to create a wide range of items, including jewelry, sculptures, and decorative objects.
The Wirework Process
1. Choosing Wire:
o Material: Wire is available in a variety of materials, including metal (such as copper, silver, and gold), aluminum, and steel. The choice of material will depend on the desired strength, durability, and appearance of the finished piece.
o Gauge: The gauge of the wire refers to its thickness. A smaller gauge indicates thinner wire, while a larger gauge indicates thicker wire. The choice of gauge will depend on the desired level of detail and the strength required for the piece.
2. Design Planning:
o Sketching: The desired design is often sketched out or drawn on paper. This helps to visualize the final product and plan the necessary steps.
o Template Creation: For more complex designs, a template may be created to guide the shaping of the wire.
3. Shaping and Bending:
o Tools: Wirework tools, such as pliers, cutters, and mandrels, are used to shape and bend the wire.
o Techniques: Various techniques can be used to shape wire, including twisting, coiling, looping, and weaving.
o Forming: The wire is bent and shaped to create the desired design. This may involve creating curves, angles, or intricate patterns.
4. Joining:
o Connecting pieces: Different pieces of wire can be joined together using various techniques, such as soldering, crimping, or wrapping.
o Creating closures: For jewelry pieces, a closure (such as a clasp or hook) is often added to secure the piece.
5. Finishing:
o Polishing: The finished piece may be polished to remove any scratches or imperfections.
o Patina: For some metals, a patina (a surface finish that can give the metal a unique color or texture) may be applied.
Applications of Wirework
• Jewelry: Wirework is commonly used to create necklaces, bracelets, earrings, and rings.
• Sculpture: Wire can be used to create sculptures of various sizes and shapes.
• Home decor: Wirework can be used to create decorative objects, such as wall hangings, candle holders, and bookends.
• Art: Wirework can be used to create artistic expressions, such as abstract sculptures or installations.
Wirework is a versatile and rewarding craft that allows for the creation of unique and personalized pieces. With practice and creativity, anyone can learn to work with wire and create beautiful and functional items.
Forging
Forging is a metalworking process that involves shaping metal into a desired form by hammering or pressing it while it is hot. This technique has been used for centuries to create a wide variety of metal objects, from weapons and tools to decorative items and jewelry.
The Forging Process
1. Heating: The metal to be forged is heated to a high temperature, typically between 1,400 and 2,200 degrees Fahrenheit, depending on the type of metal. This softens the metal, making it more malleable and easier to shape.
2. Shaping: The heated metal is then shaped using a hammer or a press. The hammer can be used to strike the metal directly, or it can be used to drive a die or punch into the metal. A press can be used to apply more force to the metal, allowing for more complex shapes to be created.
3. Finishing: Once the metal has been shaped to the desired form, it is often cooled and then finished. This may involve polishing, grinding, or engraving the metal.
Types of Forging
• Hot forging: This is the most common type of forging and involves shaping the metal while it is hot.
• Cold forging: This involves shaping the metal while it is cold. It is typically used for softer metals and simpler shapes.
Advantages of Forging
• Strength: Forging can produce metal objects that are very strong and durable.
• Versatility: Forging can be used to create a wide variety of shapes and sizes.
• Customization: Forging allows for a high degree of customization, as the metal can be shaped to meet specific requirements.
Applications of Forging
• Manufacturing: Forging is used to manufacture a wide range of products, including automotive parts, tools, and machinery.
• Art and crafts: Forging is used to create decorative objects, such as sculptures, jewelry, and metalwork.
• Restoration: Forging can be used to restore damaged or worn-out metal objects.
Forging is a time-honored technique that continues to be used today to create beautiful and functional metal objects. The ability to shape metal into complex forms and to produce strong and durable products makes forging a valuable skill for metalworkers and craftsmen.
Enameling
Enameling is a decorative technique that involves applying a colored glass paste, known as enamel, to a metal surface and then firing it in a kiln to fuse it with the metal. This process creates a durable, colorful, and often translucent coating that can be used to decorate a wide variety of metal objects, including jewelry, tableware, and decorative arts.
The Enameling Process
1. Metal Preparation:
o Cleaning: The metal surface is thoroughly cleaned to remove any dirt, grease, or other contaminants.
o Engraving or Etching: In some cases, the metal surface may be engraved or etched to create a design or pattern. This will help the enamel adhere more securely.
2. Enamel Application:
o Paste: The enamel is applied to the metal surface in the form of a paste. The paste can be applied using a variety of techniques, including brushing, dipping, or spraying.
o Multiple Layers: Multiple layers of enamel can be applied to create different colors, textures, and effects.
3. Firing:
o Kiln: The enameled metal is placed in a kiln and heated to a high temperature, typically between 1,200 and 1,500 degrees Fahrenheit.
o Fusing: During the firing process, the enamel melts and fuses with the metal surface, creating a durable bond.
4. Finishing:
o Polishing: After firing, the enameled piece may be polished to remove any imperfections and to enhance its shine.
Types of Enameling
• Cloisonné: In this technique, metal wires are used to create compartments or cloisons on the metal surface. The compartments are then filled with enamel and fired.
Cloisonné enameling
• Champlevé: In this technique, a design is etched or engraved into the metal surface, and the depressions are filled with enamel.
Champlevé enameling
• Enamel painting: This technique involves applying enamel directly to the metal surface using a brush or other tool.
Enamel painting
• Fusing: In this technique, pieces of glass or enamel are placed on a metal surface and then fired in a kiln. The glass or enamel will melt and fuse with the metal.
Enameling fusing
Applications of Enameling
• Jewelry: Enameling is commonly used to decorate jewelry pieces, such as rings, pendants, and bracelets.
• Tableware: Enameled tableware, such as bowls, plates, and cups, is often used for decorative or ceremonial purposes.
• Decorative Arts: Enameling is used to create a variety of decorative objects, including vases, boxes, and sculptures.
• Art: Enameling can be used as a medium for artistic expression, with artists creating intricate and colorful designs.
Enameling is a beautiful and versatile technique that allows for the creation of unique and durable metal objects. The ability to combine metal with colorful and translucent enamel creates a wide range of possibilities for artists and craftsmen.
Summary
This comprehensive guide delves into the world of traditional jewelry making, showcasing the timeless techniques that have shaped the industry for centuries. We’ll explore the art of casting, the precision of soldering, the intricate designs of engraving, the delicate process of setting gemstones, and the creative possibilities of beading. These methods, often combined with modern technology, continue to produce exquisite and enduring pieces that are cherished for their beauty and craftsmanship.
Related Posts
Fall in Love with Jewelry, Stories, and Secrets
Join Artemies Magazine for insider jewelry tips, trend updates, and subscriber-only discounts.
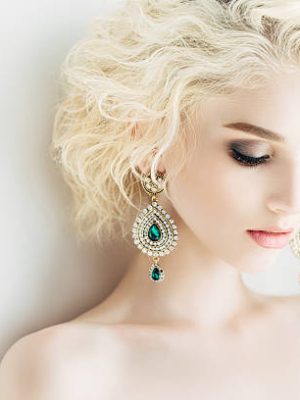