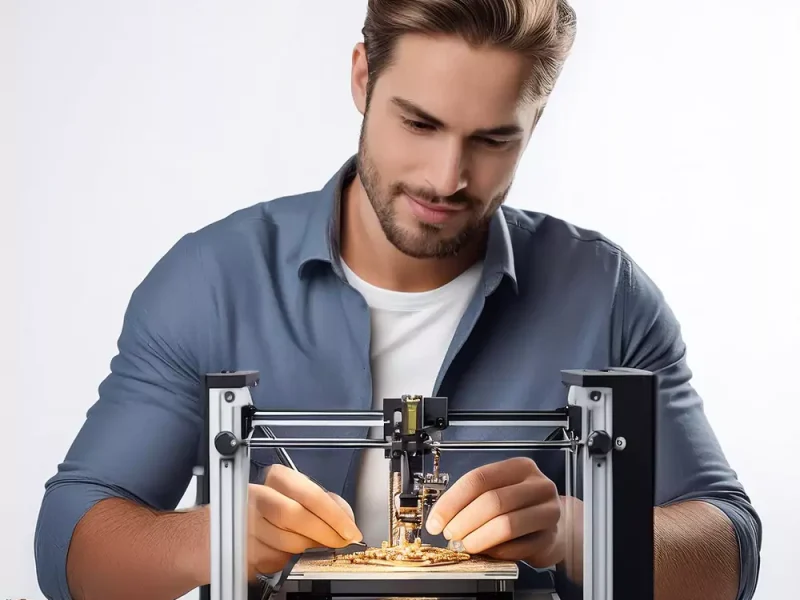
- Jewelry
Gadget Glam: How Technology is Revolutionizing Jewelry
Table of Contents
1. 3D Printing: A Detailed Explanation
3D printing, also known as additive manufacturing, is a revolutionary technology that allows for the creation of three-dimensional objects from digital designs. Unlike traditional manufacturing methods that involve removing material (such as machining or casting), 3D printing adds material layer by layer to build up the desired object.
1.1.The 3D Printing Process
1. Digital Design: The desired object is designed using computer-aided design (CAD) software. This software creates a digital model of the object, specifying its shape, size, and internal structure.
2. Slicing: The digital model is sliced into thin, horizontal layers. These layers serve as instructions for the 3D printer on how to build the object.
3. Material Deposition: The 3D printer uses a nozzle or other mechanism to deposit material onto a build platform. The material is typically heated or cooled to solidify as it is deposited.
4. Layer-by-Layer Construction: The printer builds the object layer by layer, following the instructions from the sliced model. Each layer is allowed to solidify before the next layer is added.
5. Finishing: Once the object is complete, it may require additional finishing steps, such as removing supports or sanding, to achieve the desired surface quality.
2.1.Types of 3D Printing Technologies
• Fused Deposition Modeling (FDM): This is one of the most common 3D printing technologies. It involves extruding heated plastic filament through a nozzle and depositing it layer by layer.
• Stereolithography (SLA): This technology uses a laser to solidify a liquid resin layer by layer, creating a highly detailed and accurate object.
• Selective Laser Sintering (SLS): This technology uses a laser to fuse powdered material, such as nylon or metal, together layer by layer.
• Selective Laser Melting (SLM): Similar to SLS, SLM uses a laser to melt metal powder, creating strong and durable metal parts.
3.1.Advantages of 3D Printing
• Complexity: 3D printing can create complex geometries and intricate details that would be difficult or impossible to achieve with traditional manufacturing methods.
• Customization: 3D printing allows for highly customized products, as designs can be easily modified and adapted.
• Rapid Prototyping: 3D printing enables rapid prototyping, allowing designers and engineers to quickly create physical models of their designs for testing and evaluation.
• On-Demand Production: 3D printing can be used for on-demand production, reducing the need for large inventories of finished products.
3D printing has revolutionized various industries, including manufacturing, healthcare, aerospace, and automotive. Its ability to create complex and customized objects has opened up new possibilities for design, innovation, and production.
2. Laser Cutting: A Detailed Explanation
Laser cutting is a manufacturing process that uses a focused laser beam to cut through materials, such as metal, wood, plastic, and fabric. The laser beam is generated by a high-power laser and is directed at the material to be cut. The intense heat of the laser beam melts or vaporizes the material, creating a precise and clean cut.
1.2. The Laser Cutting Process
1. Design Creation: The desired design or pattern is created using computer-aided design (CAD) software. This software generates a digital file that contains the exact dimensions and shape of the cut.
2. Laser Beam Generation: A high-power laser, such as a carbon dioxide laser or a fiber laser, is used to generate a focused beam of light.
3. Material Positioning: The material to be cut is placed on a cutting table and aligned with the laser beam.
4. Cutting: The laser beam is directed at the material, and the intense heat melts or vaporizes the material, creating a cut. The laser beam can be moved to create complex shapes and patterns.
5. Finishing: After cutting, the material may require additional finishing, such as polishing or deburring, to achieve the desired surface quality.
2.2.Advantages of Laser Cutting
• Precision: Laser cutting can produce highly precise cuts with minimal tolerances, making it ideal for applications that require accuracy.
• Versatility: Laser cutting can be used to cut a wide variety of materials, including metals, plastics, wood, and fabric.
• Speed: Laser cutting is a relatively fast process, allowing for efficient production of parts.
• Complexity: Laser cutting can create complex shapes and patterns that would be difficult or impossible to achieve using traditional cutting methods.
• Minimal Waste: Laser cutting produces minimal waste, as the material is cut precisely to the desired shape.
3.2.Applications of Laser Cutting
• Manufacturing: Laser cutting is used in a wide range of industries, including automotive, aerospace, electronics, and construction. It is used to create parts for products such as cars, airplanes, computers, and buildings.
• Prototyping: Laser cutting is used to quickly create prototypes of new products, allowing designers and engineers to test and refine their designs.
• Art and Craft: Laser cutting is used to create custom art pieces, such as jewelry, sculptures, and home decor items.
• Medical Devices: Laser cutting is used to create precise components for medical devices, such as prosthetics and surgical instruments.
Laser cutting is a versatile and efficient technology that has revolutionized the manufacturing industry. Its ability to create complex shapes, precise cuts, and minimal waste has made it an essential tool for a wide range of applications.
3. CAD/CAM in Jewelry Manufacturing
CAD/CAM (Computer-Aided Design/Computer-Aided Manufacturing) is a powerful technology that has revolutionized the jewelry manufacturing process. By combining design and manufacturing capabilities, CAD/CAM software allows jewelers to create intricate and accurate designs, streamline production, and reduce costs.
1.3. CAD (Computer-Aided Design)
• Digital Modeling: Jewelers use CAD software to create digital models of their jewelry designs. These models can be three-dimensional (3D) or two-dimensional (2D), depending on the complexity of the design.
• Customization: CAD software allows jewelers to easily customize designs, experiment with different shapes, sizes, and materials, and make changes on the computer screen before committing to physical production.
• Visualization: CAD software provides a visual representation of the final product, helping jewelers to visualize the design and identify potential issues or areas for improvement.
2.3.CAM (Computer-Aided Manufacturing)
• Machine Control: CAM software generates instructions for computer-controlled machines, such as CNC (Computer Numerical Control) milling machines or 3D printers. These machines can then automatically fabricate the jewelry pieces based on the digital design.
• Automation: CAM software can automate many of the manufacturing processes, reducing the need for manual labor and improving efficiency.
• Accuracy: CAM software ensures high levels of accuracy and precision in the manufacturing process, resulting in consistent and high-quality jewelry pieces.
3.3.Benefits of CAD/CAM in Jewelry Manufacturing
• Increased Efficiency: CAD/CAM can significantly streamline the jewelry manufacturing process, reducing lead times and improving productivity.
• Improved Accuracy: By automating many of the manufacturing processes, CAD/CAM can help to improve the accuracy and consistency of jewelry pieces.
• Cost Reduction: CAD/CAM can help to reduce costs by minimizing waste, improving efficiency, and automating labor-intensive tasks.
• Design Flexibility: CAD/CAM software allows for greater design flexibility, enabling jewelers to experiment with new shapes, styles, and materials.
• Reduced Prototyping Time: CAD/CAM can be used to create digital prototypes of jewelry designs, reducing the need for physical prototypes and speeding up the design and development process.
In conclusion, CAD/CAM technology has become an essential tool for modern jewelry manufacturers. By combining design and manufacturing capabilities, CAD/CAM software enables jewelers to create innovative and high-quality jewelry pieces while improving efficiency, reducing costs, and enhancing the overall manufacturing process.
4. Summary
This comprehensive guide explores the innovative techniques revolutionizing jewelry manufacturing. We begin by examining the magic of 3D printing, a process that builds objects layer by layer, allowing for complex designs previously deemed impossible. We then unveil the power of laser cutting, a technology that utilizes a focused laser beam to create precise and clean cuts on various materials. Finally, we delve into the world of CAD/CAM, a powerful software combination that streamlines the design and manufacturing process, fostering increased efficiency and accuracy. By understanding these modern techniques, you’ll gain a deeper appreciation for the artistry and innovation behind the exquisite jewelry pieces you see today.
Related Posts
Fall in Love with Jewelry, Stories, and Secrets
Join Artemies Magazine for insider jewelry tips, trend updates, and subscriber-only discounts.
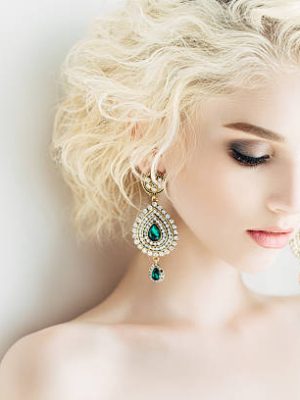